A PLC (Programmable Logic Controller) is an industrial digital computer designed to control manufacturing processes. It was developed to replace complex systems of relays and timers used in early automation. Its main purpose is to automate specific machine functions and production lines.
A typical PLC setup includes a CPU (Central Processing Unit), input/output modules, and memory. Input modules receive signals from sensors, switches, and other devices, while output modules send commands to actuators, motors, valves, and indicator lights. The CPU processes logic from the program and makes decisions based on input data.
One of the biggest strengths of a PLC is its durability and reliability in tough industrial environments. It’s built to withstand dust, moisture, vibrations, and extreme temperatures. PLCs are also fast, which is critical for real-time process control. On top of that, they’re flexible—programs can be easily changed or updated as production needs evolve. Modern factory automation simply wouldn’t exist without PLCs.
They’ve played a key role in boosting efficiency, reducing costs, and improving safety in manufacturing. Today’s PLCs are more powerful and better integrated with systems like HMI (Human Machine Interface) and SCADA (Supervisory Control and Data Acquisition). They’re the foundation of Industry 4.0 and smart factories.
But even with all those advantages, traditional PLCs still rely on wired infrastructure—optical or copper—because that’s been the only option capable of meeting the real-time data speed, latency, and quality of service demands. The downside? Wired systems can make it hard to scale or extend PLC modules to remote locations where such infrastructure doesn’t exist.
5G
Industry 4.0 demands massive device connectivity, and 5G networks are built for exactly that—with support for millions of IoT (Internet of Things) devices per square kilometer.
5G’s ultra-low latency enables real-time operations that are essential for autonomous robots, vehicles, and mission-critical process control.
Smart factories generate huge amounts of data from high-res cameras, sensors, and digital twins. 5G delivers the bandwidth needed to transmit it all quickly and reliably.
In industries where every second of downtime costs money, 5G offers reliability close to wired networks—crucial for automation and critical operations.
By replacing fixed cables with wireless 5G, manufacturers can easily rearrange machines and reconfigure production lines—cutting installation and maintenance costs.
Many companies are now deploying private 5G networks within their facilities to ensure high levels of security, reliability, and control over their data and communications.
Sensors connected via 5G can stream real-time machine data, enabling predictive maintenance before problems arise—minimizing unplanned downtime.
Ultimately, 5G is a key enabler for fully realizing Industry 4.0. It transforms traditional plants into intelligent, connected, and highly automated manufacturing ecosystems.
PLC and 5G
Thanks to its high bandwidth and low latency, 5G is emerging as a serious alternative to wired infrastructure for real-time PLC control in Industry 4.0.
Current solutions on the market use VxLAN technology to transmit PLC Profinet Ethernet packets over 5G IP networks. The architecture (shown in the diagram) encapsulates Profinet Ethernet packets into VxLAN/UDP/IP packets, which adds headers and processing delay.

Also, these packets are routed over an L3 network, adding more delay. Still, this setup is already good enough for most existing industrial use cases.
The 5G network also adds its GTP/IP headers to connect the 5G base station with the core network. At the moment, there’s no way to optimize this level due to the constraints of global 3GPP telecom standards.
However, for applications where every millisecond counts, 5G technology allows Profinet Ethernet packets to be transmitted transparently over the 5G network without L3 routing or extra VxLAN/UDP/IP headers. This significantly speeds up data transfer and essentially extends the LAN across the 5G link to reach remote devices.
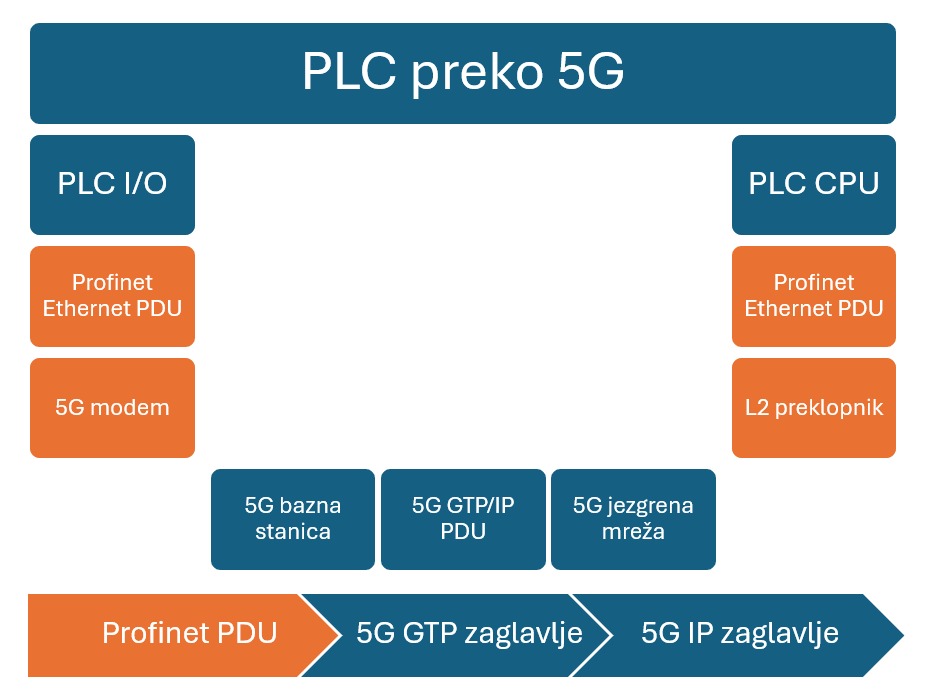
This solution is currently in testing, as it depends on support for 5G Ethernet PDU in both the end devices and the network itself.
The next step in optimization is leveraging 5G URLLC (Ultra Reliable Low Latency Communication) on the radio interface, which is the main contributor to transmission delays.
One key URLLC feature is grant-free access, also known as “configured grants.” In this setup, the 5G base station (gNB) pre-allocates specific radio resources for the user equipment (UE), allowing devices to send data immediately without waiting for a transmission grant—drastically cutting latency.
Markoja
Markoja has a long-standing history in deploying and maintaining 5G systems. The company owns the spectrum needed for private 5G networks and has its own reference solutions in this space.
Markoja offers full-service 5G solutions—from on-site assessments and business case development to deployment and ongoing support.